Global Prefabricated Buildings Market to Reach $153. 7 Billion by 2026.Prefabricated homes ,prefab houses are those that have been constructed with the help of prefabricated building materials.
These building materials are prefabricated in facility,and then transported to the desired location where they are assembled. Prefabricated houses are a combination of traditional house and technology. And at least 70% prefabricated building are known as modular house.This makes taking apart, transportation and building of these homes easy. Compared to traditional houses, prefab houses are cheaper, more sustainable and better looking. The construction materials used in developing prefab houses are classified as concrete based and metal fabricated.
Amid the COVID-19 crisis, the global market for Prefabricated Buildings estimated at US$106.1 Billion in the year 2020, is projected to reach a revised size of US$153.7 Billion by 2026.
he Prefabricated Buildings market in the U.S. is estimated at US$20.2 Billion in the year 2021. The country currently accounts for a 18.3% share in the global market. China, the world second largest economy, is forecast to reach an estimated market size of US$38.2 Billion in the year 2026 trailing a CAGR of 7.9% through the analysis period. Among the other noteworthy geographic markets are Japan and Canada, each forecast to grow at 4.9% and 5.1% respectively over the analysis period. Within Europe, Germany is forecast to grow at approximately 5.5% CAGR while Rest of European market (as defined in the study) will reach US$41.4 Billion by the close of the analysis period.
In addition,starting from 2021, the prefabricated investment market has been buzzing, and the capital sector has led and followed suit in prefabricated interior companies in China.
Authoritative analysis from the investment and financial circles believes that today, when China's industrialization has penetrated into all aspects of society (such as automobiles with an average of more than 20,000 parts and components have already been industrialized, and even Chinese restaurants with complex production processes and rich cuisines have been fully industrialized), The concept of technology decoration - prefabricated decoration is increasingly recognized by capital, and the decoration industry in 2021 is developing rapidly in the direction of Industry 4.0.
This new blue ocean market technology decoration (assembly decoration) , not only under the huge market capacity stable return expectations, but also innovative market, emerging market segments brought new opportunities and huge capital imagination space.
How big is the market? Let the numbers speak for themselves:
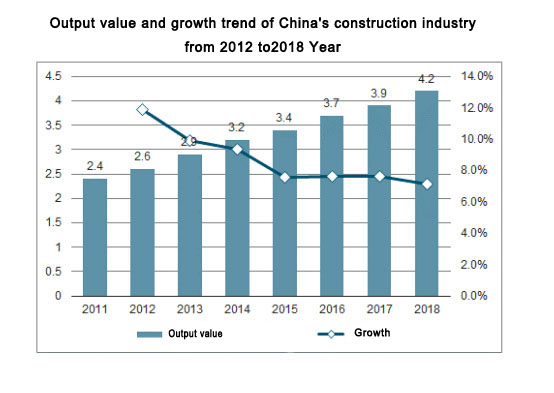
It can be seen from the data analysis that the traditional building industry still maintains a strong development. At a time when the global epidemic control is expected to improve in 2021 and the domestic economic cycle is accelerating, the growth rate of the traditional house industry is expected to be more eye-catching.
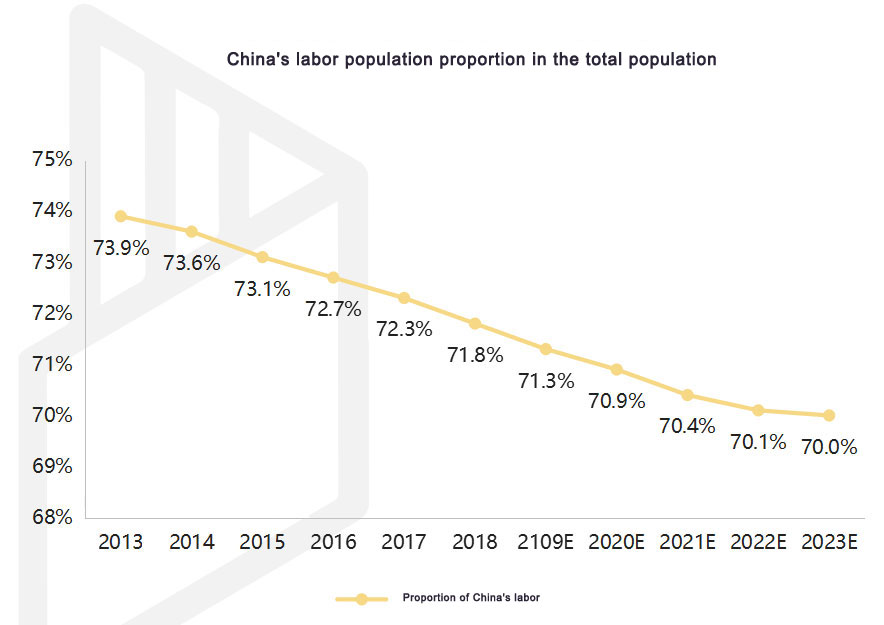
Of course, some doubts will inevitably follow: the market is so large and the growth rate continues, today's traditional house is still hot and the wave has not yet subsided, why is the prefabricated house becoming the most burning track in the industry ? What is the deep reason behind it?
1.Industry Insights: Industrial Workers Decline Year by Year
According to public data, the total number of employees in traditional building increased from 11 million in 2005 to 16.3 million in 2016; but from 2017, the number of employees in the industry began to decline. As of the end of 2018, the number of employees in the industry reached 1,300. more than 10,000 people.
2.The demographic dividend of industry insights disappears
As shown in the figure above, it can be seen that the labor force continues to decline. How many laborers are willing to enter the traditional building industry in the future? The situation is rather gloomy.
The demographic dividend is clearly declining year by year, and there is also the real dilemma of the continuous aging of employees, and traditional building is precisely a typical labor-heavy industry.
In the traditional wet decoration, each decoration site is a small production workshop, and the quality of the products depends on the craftsmanship of the construction personnel in each process such as water, electricity, wood, tile, and oil.
From the most traditional decoration to the Internet decoration that attracted the market focus in the past few years, the way the inflow of marketing customers has indeed changed (from offline to online), but in fact, the process and links of services have not undergone qualitative changes. , Each process still relies on traditional construction personnel, which is time-consuming, has many links, heavy decision-making, and long processes. These bottleneck problems have not been substantially reversed.
Under such circumstances, the prefabricated building that directly changes the production method has created a brand-new production and service model. It is conceivable how hugely disruptive it will be to the entire industry.
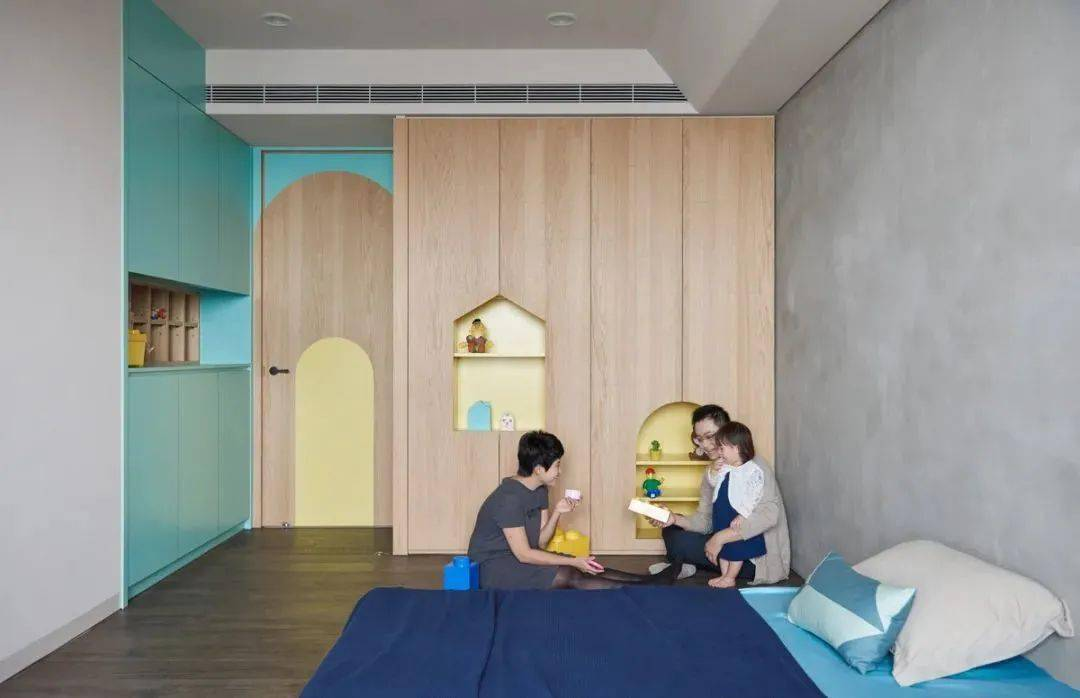
3.The prefabricated building sword of industry insight refers to the industry change
Many entrepreneurs who have inspected Japanese prefabricated buildings and decoration pointed out that Japan has developed prefabricated buildings far earlier and more complete than China, and has very standardized standards and implementation systems in terms of building standards and material standards. As an aging society in the earthquake-prone belt, Japan is facing an aging population and a sharp decline in industrial workers that are far more prominent than those in China today.
On the other hand, in China, since the initial rapid development of urbanization in the 1990s, a large number of migrant workers have poured into the city to provide cheap labor for building decoration. At that time, the prefabricated technology was relatively backward, and there were many quality problems, which led to the concept of prefabricated being forgotten for a time.
Since 2012, with the increase of labor costs and the concept of housing industrialization, the prefabricated type has been strongly supported by national policies, and the development of the industry has continued to heat up.
According to the "13th Five-Year Plan" Prefabricated Building Action Plan of the Ministry of Housing and Urban-Rural Development, by 2020, the proportion of prefabricated buildings in the country will reach more than 15% of new buildings. In 2021, more new policies will continue to be introduced and implemented.
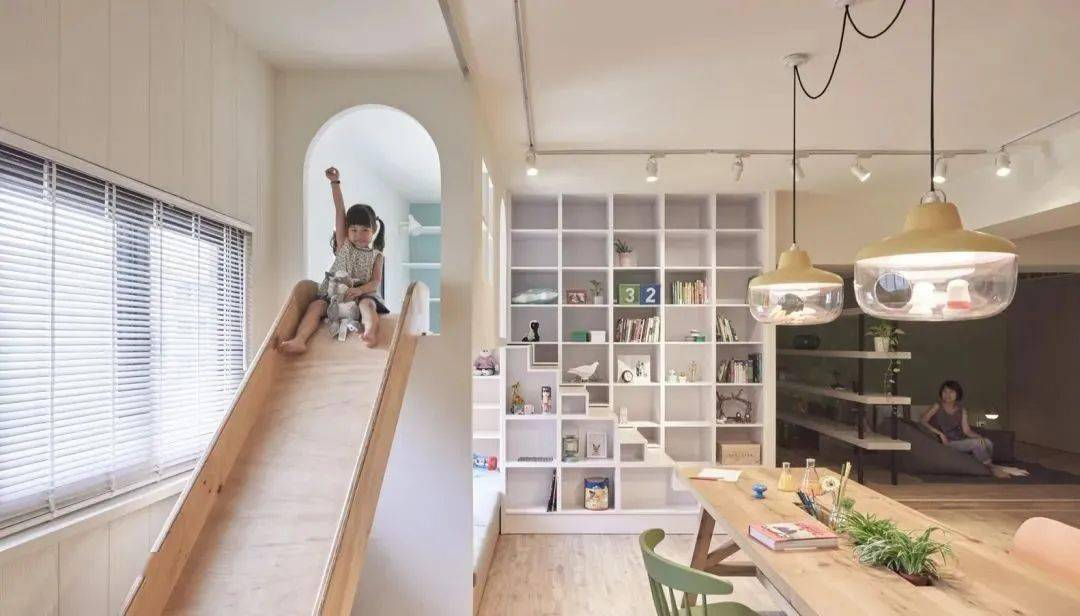
4.Industry Insights What is prefabricated building?
Prefabricated building, also known as industrial building. In 2017, the "Technical Standards for Prefabricated Concrete Buildings" and "Technical Standards for Prefabricated Steel Structure Buildings" promulgated by the Ministry of Housing and Urban-Rural Development clearly defined prefabricated decoration, itis The combined installation method which refers to the use of dry construction methods to place factory-produced interior parts on site.
The prefabricated decoration has the industrialized thinking of standardized design, industrialized production, prefabricated construction, and information-based coordination.
(1) Dry construction method is to avoid wet operations such as gypsum putty leveling, mortar leveling, and mortar bonding used in traditional decoration methods, and instead use anchor bolts, supports, structural adhesives and other methods to achieve Support and connection structure.
(2) The pipeline is separated from the structure, that is the equipment and pipeline are not pre-buried in the house structure, but filled in the gap between the six wall panels of the prefabricated houses and the supporting structure.
(3) Parts integration Customized parts integration is to integrate multiple scattered parts and materials into one organism through specific manufacturing supply, and achieve dry construction while improving performance, which is easy to deliver and assemble. Parts customization emphasizes that although prefabricated decoration is industrialized production, it still needs to meet personalized customization, so as to avoid on-site secondary processing.
5.Prefabricated building of "heavy factory and light site" of industry insight
(1)Pay attention to the pre-position of design and construction.
Preceding the design stage is to significantly improve the design capability requirements for the integration of building structure and decoration. Building Information Modeling (BIM) is an important auxiliary tool for building integrated design. For enterprises with technical accumulation in BIM, they will be able to better reflect their competitive advantages in the prefabricated decoration industry competition.
Preceding the construction stage, cross-construction with the main structure. In the traditional decoration method, all construction operations are completed on-site, while the prefabricated decoration divides the original construction work into two parts: the production of factory parts and the on-site installation. Compared with the traditional method.
(2)High quality material
The prefabricated building divides the traditional building into a variety of parts, and the decoration company provides several options for each part, thus forming the individualization in the standardization, so the product selectivity is "more".
Parts are manufactured in the factory and only installed on site. The precision of decoration is greatly improved, the influence of human factors is greatly reduced, the quality of decoration is easier to guarantee, and the quality of parts is better and more balanced.
(3)The whole process is more environmentally and healthier.
As the material, the prefabricated parts are all factory-produced, no wet work is involved, and the material is more environmentally and healthier.
The construction site is only for parts installation, all constructed by dry construction without secondary processing. Therefore, the construction period is greatly shortened compared with the traditional method. This is the case in the current first- and second-tier city hotel renovations, office quick renovations, and high turnover of real estate and residential projects. Very eye-catching positive factors, and from the perspective of the future consumption of the Customer, if the future home decoration and renovation, the materials are environmentally friendly, healthy and the construction speed is very efficient, how can it not be more popular on the Customer?
6.Industry insights predict the market size to exceed 100 billion USD
According to relevant calculation models, it is estimated that the scale of China's prefabricated building market will reach 100 billion USD in 2025, with an annual compound growth rate of 38.26%.
The market size has exceeded 100 billion USD. With such a huge new technology track, what kind of company can outperform the whole process and lead the development of the industry?
The industry generally believes that only large-scale integrated enterprises with top-level design capabilities (that is, national, local, and industry standard-setting capabilities), design and R&D capabilities, BIM technology, parts production and supply capabilities, and industrial worker training capabilities can be in this field. Stand out in the new technology track.
Coincidentally, GS housing is belong to this kind integrated enterprise.
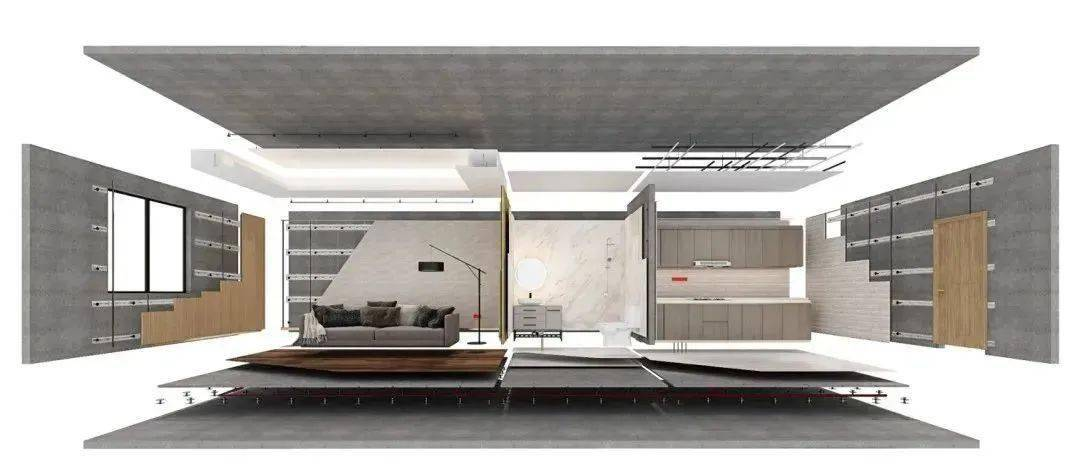
Post time: 14-03-22